A Comprehensive Guide to Identifying, Preventing, and Correcting Undercut Welding Troubles in Your Welding Tasks
In the realm of welding, coming across undercut concerns is an usual obstacle that can jeopardize the structural integrity and total quality of your welding jobs. Stay tuned as we discover the necessary components of recognizing, avoiding, and dealing with undercut welding problems, supplying you with useful understandings and approaches to raise your welding skills to the next degree.
Typical Causes of Undercut Welding
Undercut welding, a typical problem in welding processes, can be created by various aspects that need to be meticulously recognized and resolved to guarantee the integrity of the weld joint. One of the main reasons for undercut welding is too much warmth input. When the welding specifications, such as voltage, present, or take a trip rate, are not correctly established, an extreme quantity of heat can be generated. This excess warmth brings about the melting and subsequent elimination of the base material along the sides of the weld joint, producing a groove called undercut.
Another typical reason of undercut welding is inappropriate welding method. Recognizing these root causes and implementing restorative steps is crucial in stopping and fixing undercut welding issues in welding tasks.
Identifying Undercut in Welds
To determine undercut properly, appropriate illumination and zoom tools are important to examine the weld joint completely. Utilizing tools such as a welding gauge or a magnifying glass can aid in discovering even the smallest undercut flaws. In addition, running a finger or a finger nail along the weld joint can often disclose undercut, as the surface may feel unequal or have a dip where the undercut exists.
Precautionary Procedures for Undercut
Having a deep understanding of the reasons of undercut in welds enables for the application of efficient precautionary procedures to preserve weld high quality and honesty. These settings need to be maximized to stop excessive heat input, which can lead to damage development.
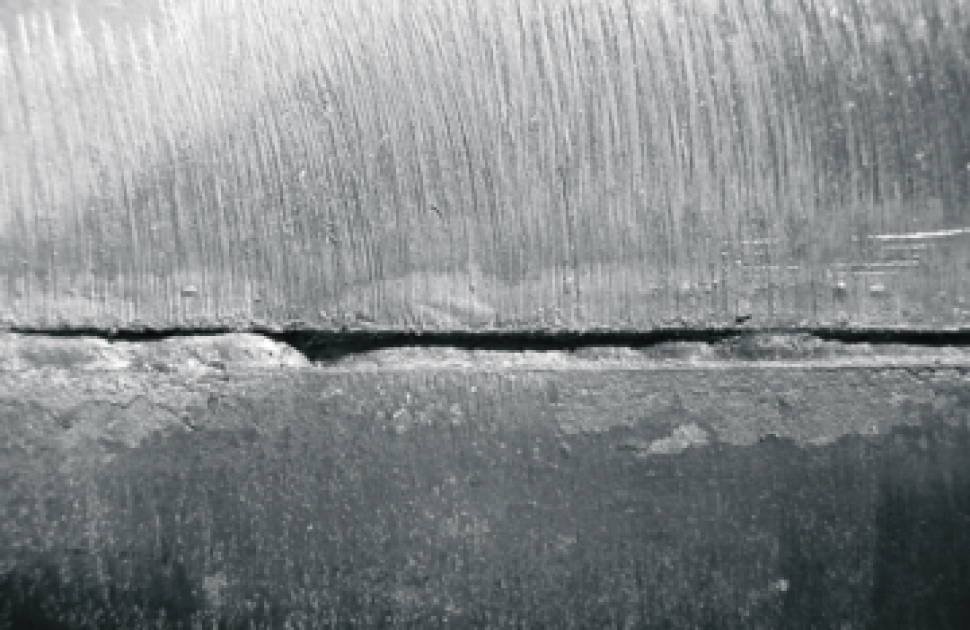
Techniques for Dealing With Undercut

Raising the welding current or reducing the travel rate can assist load in the undercut. Furthermore, transforming the welding method from a press to a drag or vice versa can likewise help decrease undercut.
Another technique is to make use of a weaving movement while welding to guarantee proper sidewall combination and fill in the article undercut. By oscillating the welding arc back and forth within the weld joint, the welder can deposit a lot more filler product into the undercut locations, properly getting rid of the problem.
Moreover, grinding out the undercut and rewelding the joint can be a feasible service for much more serious undercut concerns - Preventing weld undercut. This process includes getting rid of the undercut area, preparing the base metal, and afterwards rewelding the joint with appropriate welding parameters and strategies to avoid undercut from persisting
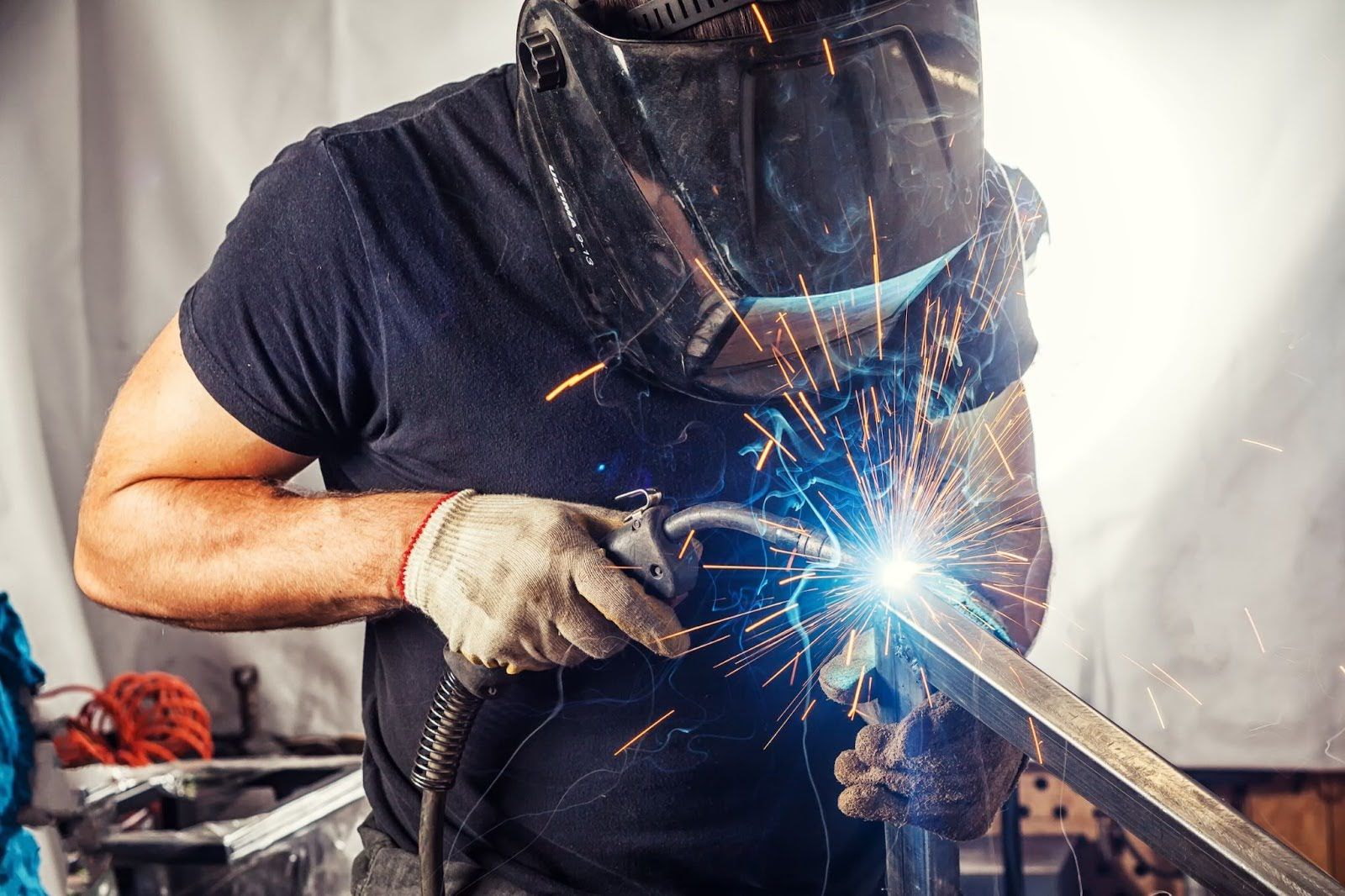
Specialist Tips for Avoiding Undercut
Using proper welding methods and keeping control over key welding parameters are essential approaches for welders intending to stop undercut in their why not find out more weld joints. Furthermore, selecting the appropriate welding procedure and filler steel for the specific application can assist protect against undercut. Keeping a regular travel rate during the welding procedure is one more essential suggestion to avoid undercut.
Final Thought
In final thought, identifying, avoiding, and dealing with undercut welding issues in your welding projects is important for making sure long lasting and solid welds. Preventing weld undercut. By understanding the common causes of undercut, having the ability to recognize it in welds, executing safety nets, and making use of appropriate methods for dealing with undercut, you can stay clear of potential issues and produce top notch welds. Complying with expert suggestions for avoiding undercut can aid you boost your welding skills and produce far better outcomes in your jobs
Undercut welding, a common problem in welding procedures, can be triggered by different elements that require to be very carefully identified and addressed to ensure the honesty of the weld joint. Furthermore, running a finger or a fingernail along the weld joint can in some cases reveal undercut, as find the surface area may feel unequal or have a dip where the undercut exists.
Using correct welding strategies and preserving control over crucial welding specifications are crucial strategies for welders aiming to protect against undercut in their weld joints.In final thought, recognizing, preventing, and dealing with undercut welding problems in your welding tasks is essential for making certain strong and resilient welds. By recognizing the usual causes of undercut, being able to recognize it in welds, implementing precautionary actions, and using correct methods for repairing undercut, you can avoid possible problems and produce top quality welds.